Knowledge Transfer Project receives top award from Innovate UK
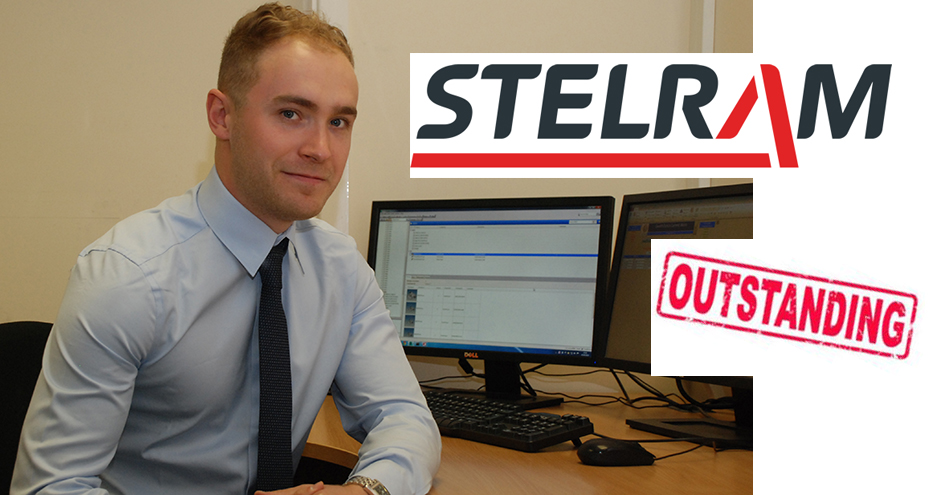
Fri, 09 Sep 2016 10:48:00 BST
The KTP scheme between the University and Stelram Engineering received the highest possible grade from Innovate UK
AN ambitious engineering firm’s expansion has been boosted by a successful collaboration with the University of Huddersfield. Now, the project has earned a mark of distinction from a Government-backed body and it will be used as an official case study.
The firm is Wakefield-based Stelram Engineering, which designs and builds bespoke machinery to carry out complex automated manufacturing tasks for sectors which include food production and the automotive industry. The company wanted to streamline its operation, cut costs in increase profits by introducing standardisation to the design process while continuing to offer tailor-made products to clients.
To achieve this, Stelram linked up with the University of Huddersfield for a Knowledge Transfer Partnership (KTP). Backed by the Government’s technology agency Innovate UK, these partnerships provide funding for a talented graduate – known as the KTP Associate – to be based within a company and carry out research, overseen by a KTP Supervisor from the academic staff of the participating university.
For the Stelram KTP, the Associate was University of Huddersfield engineering graduate Gareth Eyre, and his supervisor was Dr Simon Barrans, who is Reader in Turbocharger Engineering at the Turbocharger Research Institute, based at the University. The KTP is now complete and after an exhaustive process, Gareth has developed a bespoke database for Stelram, which acts as a components library that is consulted by the firm’s team of designers.
As the firm had grown, explained Gareth, its expanding team of designers tended to stick with their own preferences for parts, leading to a huge diversity of components being obtained and employed – and a drop-off in efficiency.
Working closely with the company’s IT manager and equipped with his degree training in mechanical engineering, Gareth used a system of taxonomic classification to rationalise the range of parts being used by Stelram.
When a Stelram designer needs a part for new bespoke machine, there is a very high likelihood that it will be found in the special new database. Gareth calculates that there have been reductions of 93 per cent in the time taken to retrieve a part. There is also enormous potential for negotiating discounts with suppliers, if they are assured that their products will become part of the standardised range use by Stelram.
In addition to working on component standardisation as part of the KTP, Gareth has also worked on process standardisation – rationalising the level of variation during product design.
Now that the Knowledge Transfer Partnership has been completed, Gareth now has a permanent role as quality engineer at Stelram, and he is completing the MSc degree that was part of the KTP.
Innovate UK has appraised the Stelram KTP and awarded the project its top grade of “Outstanding”. It has also informed Dr Barrans that it will be added to a shortlist list from which KTP case studies will be developed.
Stelram is delighted with the outcome of the KTP. Its head of HR, Lloyd Thomas, commented:
“The new robust tools and processes developed have provided us with a greater operational visibility and strategic direction which will allow for further expansion with confidence. We expect to increase our sales turnover and profits dramatically over the next three years as a direct result of the KTP.”
Dr Barrans at the University of Huddersfield praised Gareth Eyre’s achievements and the impact his research had made.
“The procedures that have been put in place have given the management confidence to take on bigger and bigger jobs and the company expanded substantially during the actual KTP. It has enabled them to achieve their goals and set themselves even more ambitious targets for the future.”
- Founded three decades ago, Stelram has recently expanded its production facilities to 27,000 square feet. It has become one of the UK’s leading suppliers of automation to the food and drink and automotive sectors, designing and manufacturing bespoke machinery and vision-controlled robotic systems.